お役立ち情報
シャフト摩耗の原因と対策|シャフトをコストメリット良く活用するためには?
2024/12/12
- シャフト
- 長寿命化
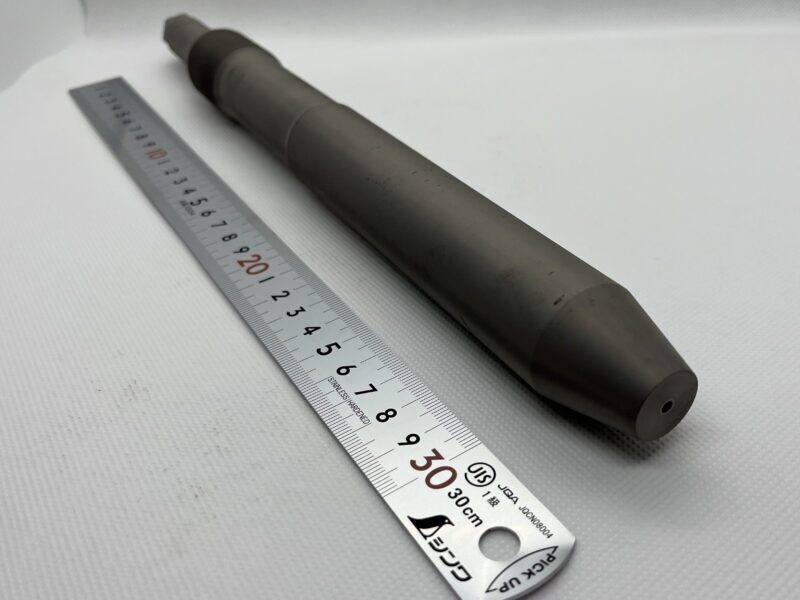
目次
シャフトとは?
シャフトは、動力を伝達するための回転軸として、機械の心臓部ともいえる存在です。エンジンやモーターからの回転エネルギーを機械内部の他の部品に伝え、統一された動作を実現します。例えば、コンベアの駆動軸、ポンプの回転軸、ロボットアームのジョイントなど、シャフトはあらゆる分野で不可欠な部品です。そのため、シャフトの性能が機械の稼働効率と寿命に直接的な影響を与えます。
シャフトが使用される主な産業分野
シャフトは製造業、自動車産業、航空宇宙、発電設備、農業機械など、非常に広範な分野で活用されています。特に、自動車産業ではトランスミッションや駆動系、製造業では搬送装置や精密機械の動力伝達に用いられます。また、発電分野ではタービンシャフトとしての役割も重要です。各産業で求められるシャフトの特性は異なるため、用途に応じた設計と選定が鍵となります。
シャフトの素材と特性
用途に応じた適切な素材選定は、シャフトの寿命と耐久性を左右します。一般的には、炭素鋼や合金鋼が高強度と耐摩耗性から選ばれます。腐食環境ではステンレス鋼、軽量化が求められる場合はアルミニウムやチタン合金が使われます。さらに、表面硬化処理やコーティングを施すことで、耐摩耗性や耐腐食性を向上させることが可能です。
シャフトは、さまざまな産業分野で機械の中核を担う重要な部品ですが、日常的な使用環境や条件によって徐々に摩耗が進行します。摩耗はシャフトの性能や寿命に直接影響を与え、放置すると機械全体の稼働率低下や重大なトラブルの原因となります。
では、シャフトがどのような理由で摩耗し、その対策として何ができるのかを詳しく見ていきましょう。
シャフトが摩耗する原因とは?
潤滑不良
潤滑不良はシャフト摩耗の最大の原因の一つです。潤滑剤が適切に供給されない場合、シャフト表面と摩擦部分に摩擦熱が発生し、表面が損傷します。これはシャフトと軸受、またはメカニカルシール間の摩擦部分で顕著です。さらに、潤滑剤の劣化や不適切な種類の使用も摩耗を促進します。特に、高速回転する機械では潤滑システムの信頼性がシャフト寿命を左右します。
異物混入
砂や金属粉などの異物がシャフト周辺に侵入すると、シャフト表面に圧痕や傷をつける原因となります。これにより、摩耗が進行し、最終的にはシャフトの機能を損ないます。異物侵入を防ぐには、密閉システムやフィルターの導入が効果的であり、定期的な清掃と点検が欠かせません。
過大荷重
シャフトに過大な荷重がかかると、たわみやねじれが発生し、表面が劣化します。ラジアル荷重やアキシアル荷重が過剰になると、シャフトの設計寿命が短縮されます。これを防ぐには、設計段階で荷重分布を最適化し、使用条件に応じたシャフト材質や直径を選定することが重要です。
ベアリングの問題
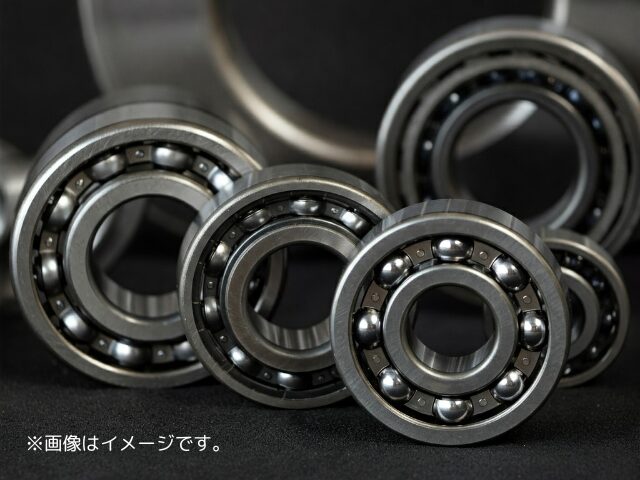
ベアリングの不具合は、シャフト摩耗の隠れた原因です。取付不良、潤滑剤の不足、または摩耗した金属ボールが原因で振動や異音が発生し、それがシャフト摩耗を引き起こします。ベアリングの適切な選定と定期的なメンテナンスがシャフトの寿命延長に貢献します。
シャフトが摩耗する主な原因は上記の通りです。では、これらの原因による摩耗はが機械全体や生産工程にどのような影響を及ぼすのでしょうか。摩耗が進行することで、シャフト自体だけでなく、関連する部品や機械全体の性能や寿命にも影響を及ぼす可能性があります。
ここでは、シャフト摩耗が引き起こす具体的な影響について詳しく見ていきます。
シャフトの摩耗がもたらす影響とは?
機械性能の低下と生産効率の低下
シャフト摩耗により表面精度が損なわれると、機械全体の動作が不安定になります。その結果、摩擦損失が増大し、生産効率の低下やエネルギーコストの増加を招きます。また、製品品質に悪影響を及ぼす可能性もあります。
部品寿命の短縮によるコスト増加
シャフトが摩耗することで、軸受やシールなどの関連部品も同時に摩耗が進み、交換頻度が増加します。このような連鎖的な損傷は、トータルのメンテナンスコストを大幅に押し上げます。
故障リスクと生産ライン停止の可能性
摩耗が進行すると、シャフトの破損や変形が発生し、生産ライン全体の停止リスクを引き起こします。このようなトラブルは、製造プロセス全体に悪影響を及ぼし、大規模な損失につながる可能性があります。
では、これらの問題を未然に防ぎ、シャフトの寿命を延ばすためには具体的にどのような対策を講じるべきなのでしょうか?
次に、シャフトの摩耗を抑制するために効果的な手法や管理方法について詳しく解説します。
シャフトの摩耗を抑制するには
適切な潤滑管理
高品質の潤滑剤を使用し、定期的な補充や交換を実施することで摩擦や摩耗熱を最小限に抑えられます。また、自動潤滑装置の導入により、潤滑管理の効率化と安定性が向上します。
異物侵入の防止
異物がシャフトに接触するのを防ぐため、密閉装置や適切なフィルターを導入します。さらに、異物混入を未然に防ぐための作業環境改善や定期的な清掃も重要です。
適切な荷重設計
使用条件を考慮した荷重分布の最適化が重要です。設計段階でラジアル荷重やアキシアル荷重を正確に計算し、必要に応じてシャフトの材質やサイズを調整することで、摩耗リスクを抑えられます。
表面処理やコーティングの活用
耐摩耗性を高めるため、窒化処理や硬質クロムメッキなどの表面処理を施すことが有効です。これにより、シャフトの寿命が大幅に向上し、交換頻度を削減できます。
定期的なメンテナンスと診断
シャフトの摩耗状態を定期的に診断することで、早期発見と対策が可能になります。特に振動や異音が発生した場合、原因を特定して迅速に対応することで、重大なトラブルを防ぎます。
シャフトの摩耗を抑制するにはこれらの対策が重要です。
では、シャフトが実際にシャフトが摩耗してしまった場合はどうするのがよいのでしょうか。
もし、シャフトが摩耗してしまったら?
シャフトが摩耗してしまった場合、迅速な対応が機械全体の安定稼働を維持する鍵となります。対応策としては、以下の3つの選択肢が一般的です:
- 再生加工:摩耗したシャフトを修復して再利用する方法。
- 長寿命化部品への交換:耐摩耗性に優れた高性能部品での交換。
- 通常通りの交換:新品の標準部品に交換する方法。
摩耗の原因や程度、使用環境、予算に応じて最適な選択肢を決定することが重要です。それぞれの方法にはメリットとデメリットがありますが、いずれにしても迅速な判断と計画的な実施が不可欠です。
シャフトの再生加工
再生加工とは、摩耗や損傷を受けたシャフトを修復し、元の性能を取り戻す方法です。加工では、摩耗部分を除去し、新たな表面を形成します。これには、溶射、研磨、メッキなどの技術が使用され、適切なコーティングで耐久性を向上させます。
再生加工の主な方法
- スリーブ圧入
摩耗部分を削り、その部分に合わせて製作したスリーブを圧入する方法です。この方法は、軸の端部で面荷れが深い場合に効果的です。 - 溶射
不具合の面荷れがΦ2.0mm以下の場合に有効な方法です。WC-12Co材などの硬質材料を摩耗部分に吹き付けます。熱影響による変形がなく、再生前の状態よりも高い耐久性が得られる利点があります。 - 溶接肉盛り
中~高荷重の場合に適しています。摩耗部分に溶接で金属を盛り、その後研削仕上げを行います。ただし、溶接時の熱影響や残留応力による曲がりや加工硬化に注意が必要です。 - 硬質クロムめっき
コスト面で優位であり、処理時の熱影響も少ない方法です。ただし、推奨膜厚が0.1mm以下の場合が多いため、摩耗が0.1mm以上進行している場合は対応できないことがあります。
再生加工のメリット
- コスト削減
新品のシャフトを購入するよりも、再生加工を行う方が一般的に安価です。特に高額な軸や廃番となった部品の場合、再生加工は経済的な選択肢となります。 - 廃棄物削減
摩耗したシャフトを再利用することで、産業廃棄物の削減に貢献します。 - 性能向上
適切な再生加工を行うことで、元の状態よりも高い耐久性を得られる場合があります。例えば、溶射による再生では、再生前の状態よりも高い耐久性が得られます。 - 短納期
新品のシャフトを製作するよりも、再生加工の方が短期間で完了する場合が多いです。
再生加工のデメリット
- 品質の不確実性
再生加工の品質は、元のシャフトの状態や加工方法によって左右されます。亀裂や曲がりを見逃した場合、再生後も強度が十分に回復しない可能性があります。 - 適用限界
摩耗の程度や使用環境によっては、再生加工が適さない場合があります。例えば、硬質クロムめっきの場合、推奨膜厚が0.1mm以下のため、摩耗が0.1mm以上進行している場合は対応できないことがあります。 - 熱影響のリスク
溶接による再生の場合、熱と残留応力により曲がりや加工硬化が発生する可能性があります。また、溶接の境目で亀裂が入るリスクもあります。 - コストの変動
再生加工のコストは、摩耗の程度や選択する加工方法によって大きく変わります。高度な技術を要する方法(例:溶射)は、コストが高くなる傾向があります。 - 性能の制限
再生加工によっては、元の性能を完全に回復できない場合があります。例えば、溶射による再生は衝撃に弱いため、使用環境を選ぶ必要があります。
当社にも実際に再生加工の依頼が来ることがあります。
特に材料が高い時や貴重な時、大きい時などは肉盛り等での再生の依頼が来ることも多いです。
しかし、シャフトの再生加工をしたとしても、摩耗具合や環境によってはまたすぐシャフトが摩耗してしまう場合もございます。
そういった場合にオススメなのが長寿命化部品への交換です。
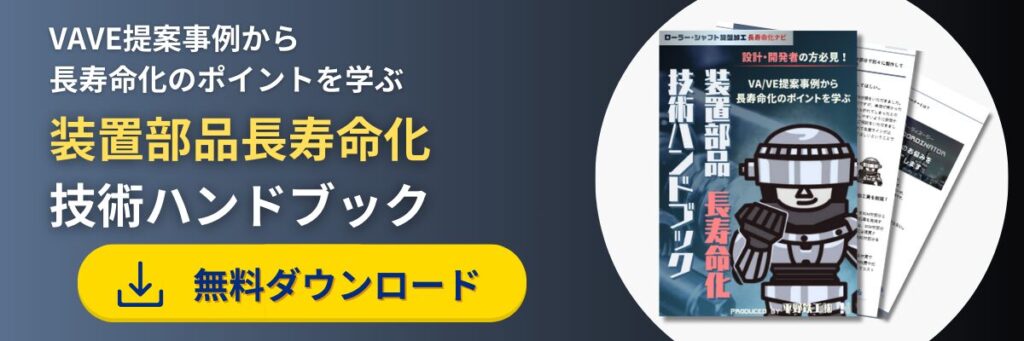
長寿命化シャフトへの交換
シャフトを再生加工しても、同じ負荷や使用環境で再び摩耗が進行することがあります。このような課題に対応するため、摩耗しにくい素材や最適な表面処理を選定し、使用条件に最適化された長寿命なシャフトを新規に製作する手法が「長寿命化部品への交換」です。これにより、交換頻度を大幅に削減し、部品や機械全体の寿命を延ばすことが可能です。
長寿命化シャフトのメリット
- 交換頻度の削減
長寿命化部品は従来品に比べて耐摩耗性に優れているため、シャフトの交換頻度を低減できます。これにより、メンテナンスコストやダウンタイムを最小限に抑えます。 - 使用環境に適応した設計
用途や使用環境に応じた素材や表面処理を選定することで、特定の条件下でも高い耐久性を発揮します。 - トータルコストの削減
初期費用は高くなる場合がありますが、交換頻度の削減や生産効率の向上により、長期的にはトータルコストを大幅に削減できます。
長寿命化シャフトのデメリット
- 初期費用
長寿命化部品は、耐摩耗性や耐久性を高めるために特殊な素材や加工が必要になるため、従来品に比べて製作コストが高くなる傾向があります。特に初回導入時には予算の確保が課題となる場合があります。 - 新規製作・納期
標準品ではなく、用途に合わせたオーダーメイドの部品となるため、設計・製作に時間がかかることがあります。急ぎの交換が必要な場合には対応が難しい場合もあります。
長寿命化シャフトの製作プロセス
- 用途と環境の分析
使用条件や負荷環境を詳細に分析し、摩耗の原因や改善点を特定します。 - 素材と表面処理の選定
耐摩耗性や耐腐食性に優れた素材を選び、適切な表面処理(窒化処理、PVDコーティングなど)を施します。 - 部品の製作と試験
設計に基づき新規シャフトを製作し、耐久性や性能を検証します。
ここまで、長寿命化部品への交換と再生加工について紹介してきました。
では、実際にシャフトが摩耗した場合、どの対応を選択するのがコストメリットが良いのでしょうか。
現行品の交換も含めて、それぞれを比較してみましょう。
シャフトの再生加工/長寿命化部品交換/現行品交換のコストメリットの比較
項目 | 長寿命化部品への交換 | 再生加工 | 現行品交換 |
初期費用 | 特殊素材や加工が必要になる場合は初期費用は高くなる。ただし、交換頻度削減を考慮するとコストパフォーマンスが高い。 | 新品購入より安価。ただし、高度な技術を伴う加工の場合はコストが増加する場合あり。 | 標準部品価格が適用されるため、中程度のコストがかかる。特別な設計や加工は不要。 |
交換頻度 | 摩耗に強い設計により交換頻度が大幅に減少。高負荷や特殊環境での使用でも長期間使用可能。 | 軽度な摩耗であれば短期間で再生が可能だが、使用環境次第で再摩耗が進行する場合あり。 | 使用頻度や環境次第で、定期的な交換が必要になるため頻度が高くなる場合がある。 |
維持費用 | 長寿命設計により部品の交換やメンテナンス頻度が減少し、維持費用が抑えられる。 | 加工精度により耐久性が異なるため、品質によっては短期間で追加の再加工が必要になるリスクあり。 | 頻繁な交換が必要な場合、交換コストが蓄積して総維持費用が高くなる可能性がある。 |
廃棄物コスト | 長寿命化による廃棄頻度の低下で廃棄コストが抑制される。 | 再利用により廃棄物が削減され、処理コストが抑えられる。環境面でも優位性あり。 | 部品交換ごとに廃棄が発生するため、長期的には廃棄処理コストが増加。 |
トータルコスト | 初期費用は高いが、交換頻度の削減やメンテナンス費用の低下により、長期的にはトータルコストが大幅に削減される。 | 初期費用が安価であるため短期的にはコストメリットが高いが、使用環境によっては追加の再加工が必要になり、長期的なコストが増加する可能性あり。 | 短期的には安価だが、交換頻度や廃棄コストの積み重ねにより、長期的なトータルコストは最も高くなる傾向。 |
初期費用 | 特殊素材や加工のため初期費用が高め。 | 新品より安価。ただし、高度な加工技術が必要な場合はコスト増加。 | 新品部品として標準価格が適用される。 |
適用性 | 高温、腐食環境など、特定の条件に合わせて最適化が可能。 | 軽度~中程度の摩耗に適しており、高度な環境には限界あり。 | 使用環境に特化した対応は難しい場合あり。 |
リスク | 設計ミスや過剰な仕様選定により、過剰コストの発生リスク。 | 熱影響や加工精度により、品質がばらつく可能性あり。 | 標準品の品質には一定の保証があるが、使用環境には適応しない場合も。 |
推奨場面 | 高負荷または特殊環境での使用、長期的なコスト削減を目的とする場合。 | 高価または廃番部品、軽度な摩耗で短納期が必要な場合。 | 一般的な運用環境で標準的なメンテナンス |
長期的なコストメリットのポイント
- 長寿命化部品への交換: 初期費用は高くなる場合があるものの、交換頻度が減少するため、長期的なコスト削減に優れています。
- 再生加工: 初期費用が低く、軽度の摩耗であれば十分なコストメリットを発揮します。ただし、使用環境が厳しい場合は再摩耗が進み、長期的なコストが増加するリスクがあります。
- 現行品交換: 初期費用と手軽さで選ばれることが多いですが、交換頻度の高さや廃棄物コストが蓄積するため、長期的には最もコストがかかる場合があります。
長期的なコスト削減を重視する場合は、長寿命化部品への交換が有効です。一方、短期的な対応が求められる場合や、軽度な摩耗で済む場合には再生加工も有力な選択肢となります。また、材料費が高い時、貴重な時、大きい時などは再生加工の方が適している場合もございます。
ローラー・シャフト旋盤加工長寿命化ナビは「長寿命化提案」にも「再生加工」にも対応しております。お客さまの使用用途、環境、要望に合わせて最もコストメリットの良い方法で提案をさせていただきますので、ぜひお気軽にご相談ください。
当社だからこそできるシャフトの長寿命化提案
当社では創業以来、当社では自動車業界の部品を中心に生産しており、特にシャフトの製造を行っておりました。シャフトは、消耗が激しい丸物加工品で、なるべく交換をせずに長く使用したいというニーズが強い一方で、精度は高くなければいけないという、要求仕様も多い製品です。当社ではこうしたシャフトに対して、歪みが少なく、高強度・高硬度を実現する焼入れ・表面処理をご提案しております。
独自の加工ネットワークであらゆる種類の処理に対応しております。これまでに培ってきた実績やノウハウをもとに、最適な表面処理のご提案を行い、シャフトの長寿命化を実現いたします。
以下に、当社が選ばれる理由を具体的にご紹介します。
耐摩耗性・高強度が必要な製品への長寿命化提案に自信あります!
当社ではローラーやシャフト、シリンダー、ピンなど、消耗が激しい丸物加工品を多く取り扱っており、これらの製品に対する長寿命化を実現する技術提案に自信があります。
創業以来、当社では自動車業界の部品を中心に生産しており、現在は産業機械装置の部品も含めて多品種少量生産を行っております。特に当社にご依頼いただくのは、消耗が激しい丸物加工品が多くなっています。ローラーやシャフトは、なるべく交換をせずに長く使用したいというニーズが強い一方で、精度は高くなければいけないという、要求仕様も多い製品です。当社ではこうした丸物部品に対して、歪みが少なく、高強度・高硬度を実現する焼入れ・表面処理をご提案しております。
一方で当社では、「とにかく硬く、長持ちするようにしたい」というお客様に対して、「あえて消耗しやすくして交換頻度は多くするが、コストを抑える」というご提案も行っております。必要以上に製品の強度や硬度を向上させると、仕上げ加工が困難となり、コストも異常なほど高くなってしまいます。そのため当社では、あえて相手部材より負けさせてコストを抑えるという提案も行っています。
当社では、金属コーディネーターとして丁寧にヒアリングを行い、お客様が本当に必要とする機能を実現するための焼入れ・表面処理を選定しております。焼入れや表面処理については、独自の加工ネットワークであらゆる種類の処理に対応しております。さらに長寿命化だけでなく、機能を改善するための形状変更や機構改善など、型にはまらない斬新なVE・VA提案を幅広い範囲で行っております。耐摩耗性や高強度が必要な丸物製品は、金属コーディネーターに一度ご相談いただければ、当社から最適な技術提案をいたします。
小径から大径まで、様々なシャフトの旋盤加工に対応
当社にご相談いただくことが多いのは、ローラーやギヤシャフト、シリンダー、ピンなどの丸物加工品です。φ5の小さいピンからφ100のピンまで、長さも様々な丸物製品に対応しております。当社が最も得意とするのは、手にのるくらいのサイズがメインです。特にΦ300~600までの、馬力がない旋盤では削ることができないような、クレーンを用いて機械にセットする必要がある、やや取り回しがしづらいような中型丸物部品について、多くのお客様からご相談をいただいております。協力会社の加工ネットワークも駆使することで、最大φ900までの比較的大径な丸物加工まで対応可能です。
さらに当社では、シャフトなどの高精度な丸物部品のご相談も多くいただいておりますが、このような製品については円筒研削(円筒研磨)による仕上げ加工まで対応しております。耐摩耗や強度が求められる丸物製品は、回転運動しながら使用される製品のため、寸法公差や真円度など、高い精度が求められます。こうした精度が必要なシャフトについても、安心して当社にお任せいただけます。
※長さ、形状、材質など各種条件によりますが、軸物の寸法公差はh7級にて基本的には対応しております。
そして形状についても、歯切り加工が必要なギヤシャフト、キー溝加工にも対応しております。小径から大径まで、高精度かつ複雑形状な製品まで、丸物加工でお困りの製品はなんでもご相談ください。
丸物加工から溶接組立まで一貫対応
当社の特徴として、丸物や角物の加工、その後の表面処理・熱処理だけでなく、溶接組立まで対応していることが挙げられます。特にΦ300以上の中型・大型フランジのような円形の丸物になると、付随した部品を溶接組立して使用するケースも多くなります。当社では、独自の外注加工ネットワークも駆使して、このような大型丸物加工品への溶接組立まで一貫対応しております。
また当社では、旋盤を中心とした丸物加工が多くなっていますが、マシニングセンタを使用した角物加工にも対応しております。機械・装置部品については角物のフレームやガイド部品も多く、溶接組立が必要な製品もあります。当社ではこうした溶接組立製品の取り回しも行っていますので、お客様の製品管理工数を削減する部品調達代行も行っています。
単品、小ロットでも短納期・特急対応
当社にご依頼いただくことが多いのは、耐摩耗・高強度で長寿命化が求められる製品です。このような製品は、生産ラインや機械装置においても重要な機構部品であることが多く、万が一修理やトラブルになった際は、すぐに必要となる製品であることが多いです。そして緊急時には、個数は200個のようなロットではなく、少数や単品での発注が多くなります。しかし単品・小ロットでの依頼は、小回り対応や緊急対応が求められるため、対応不可とお断りされるケースも多くなります。
当社では、このような他社でお断りされた単品・小ロットの製品の加工依頼を多くいただいております。特に当社の特急対応には、既存のお客様からは価値を感じていただいているポイントです。いますぐ製品を加工してほしい!という場合も、まずは金属コーディネーターの当社にご相談ください。
既存製品のコスト削減についても、製品の使用目的や環境をお伺いした上で、最適な部品設計をいたしますので、コストダウンについてもお任せください!
シャフトの加工事例
続いて、実際に当社で製作したシャフトの加工事例をご紹介いたします。
シャフト
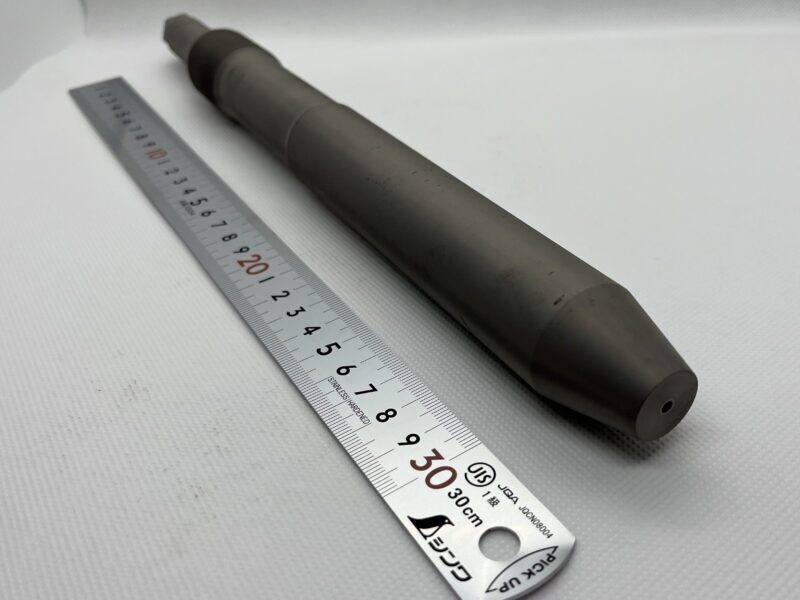
こちらは工業設備で使用されるシャフトです。サイズはΦ32×325mmで、材質はS45Cを使用しております。加工工程としては、まず旋盤加工を行い形状を作り、その後フライス加工を施し、最後に窒化処理を実施しております。
本製品は、精度(0〜-0.025)を必要としながらも、耐摩耗性を得るために窒化処理を施しております。このように、高精度と高耐久性を兼ね備えたシャフトを提供するために、精密な加工技術と最適な表面処理技術を駆使しています。
設備用シャフト
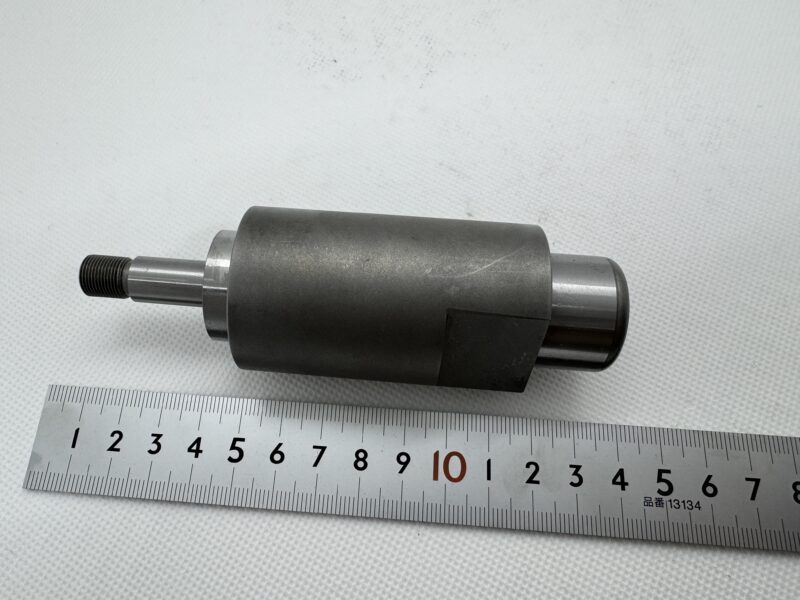
こちらは線材圧延時に使用される設備用シャフトです。サイズはΦ38×127mmで、材質はSNC415を使用しております。加工工程としては、まず旋盤加工を行い形状を作り、その後マシニング、浸炭焼入れ、そして研磨加工を実施しています。
本製品は、精度が求められるため、焼入後に研磨加工を行っています。お客様からの要望で、硬度を増したい一方で材料費も抑えたいとのことでした。そこで当社から詳細ヒアリングをさせていただき、時間がかかってもいいとのことだったため、元々は材質をS45Cで製作する予定でしたが、SNC系を使用し、焼入処理は浸炭焼入れをご提案いたしました。これにより硬度向上による長寿命化と交換頻度の低減につながり、結果としてコストダウンにもつなげることができました。
設備用段付きシャフト
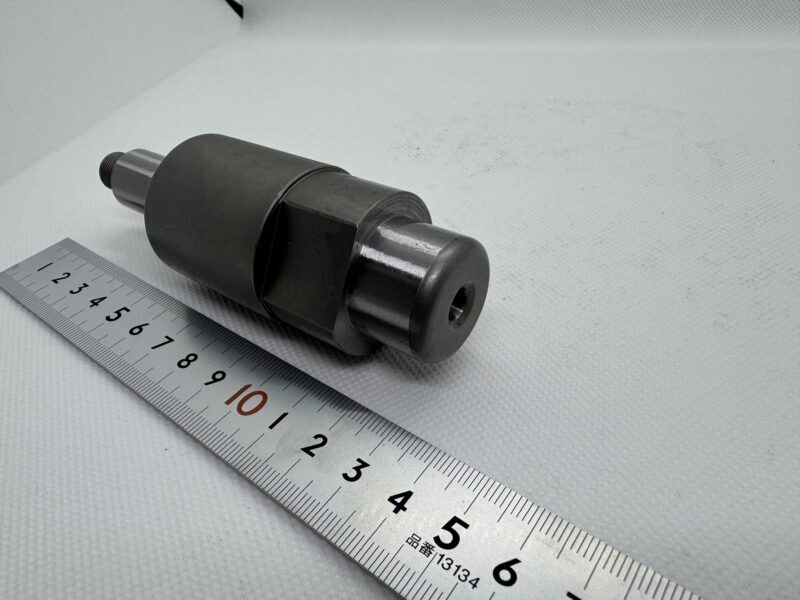
こちらは線材圧延時に使用される設備用段付きシャフトです。サイズはΦ38×127mmで、材質はSNC415を使用しております。加工工程としては、まず旋盤加工を行い段付き形状を作り、その後マシニング、浸炭焼入れ、そして研磨加工を実施しています。
本製品は、精度が求められるため、焼入後に研磨加工を行っています。お客様からの要望で、硬度を増したい一方で材料費も抑えたいとのことでした。そこで当社から詳細ヒアリングをさせていただき、時間がかかってもいいとのことだったため、材質はSNC系を使用し、焼入処理は浸炭焼入れをご提案いたしました。これにより硬度向上による長寿命化と交換頻度の低減につながり、結果としてコストダウンにもつなげることができました。
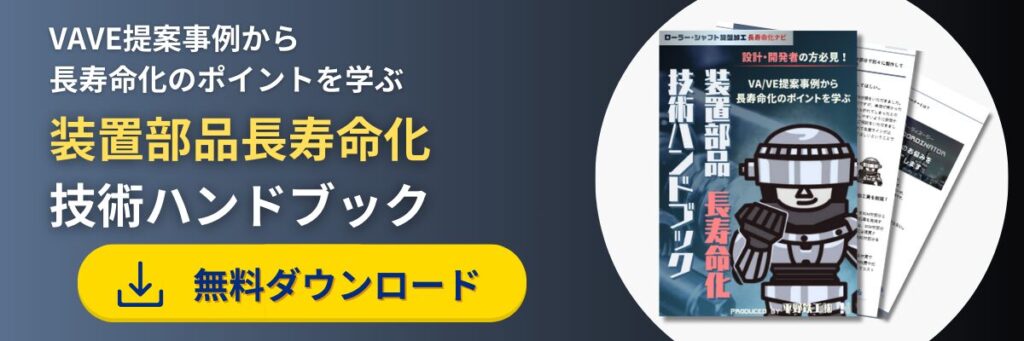
シャフトのことなら平野鉄工にお任せください!
ローラー・シャフト旋盤加工 長寿命化ナビを運営する平野鉄工株式会社は、丸物加工品を専門とし、耐摩耗性や高強度が求められる製品の長寿命化と機能向上を実現する技術提案に自信を持っています。当社の金属コーディネーターが丁寧なヒアリングを行い、焼入れや表面処理の最適な選定を行うだけでなく、形状変更や機構改善などの斬新な提案も行い、お客様にとって最適な解決策を提供します。
対応可能な製品は、直径φ5の小さいピンからφ100のピンまで、長さも様々な丸物製品に対応しております。特にΦ300~600までの、馬力がない旋盤では削ることができないような、クレーンを用いて機械にセットする必要がある、やや取り回しがしづらいような中型丸物部品について、多くのお客様からご相談をいただいております。協力会社の加工ネットワークも駆使することで、最大φ900までの比較的大径な丸物加工まで対応可能です。
ローラー・シャフト旋盤加工 長寿命化ナビでは、多様なニーズに応える高い技術力と柔軟な対応力を持ち、お客様の製品開発を強力に支援します。丸物加工品の製造において、耐久性や精度を求めるなら、ぜひローラー・シャフト旋盤加工 長寿命化ナビにお任せください。お客様のご相談をお待ちしておりますので、どうぞお気軽にお声がけください。
関連記事
-
2025.08.12
硬質クロムめっきの特性を活かすには?丸物加工品の長寿命化を実現するためのポイントを解説!
- 長寿命化
Warning: Undefined variable $news_excerpt_text in /home/xs633096/metal-processing-coordinator.com/public_html/cms/wp-content/themes/hirano-metal/assets/include/part-column-list.php on line 58
長寿命化が求められる丸物加工品にとって、硬質クロムめっきは非常に有効な表面処理です。しかし、単にめっきを施すだけでは、その特性を最大限に活かすこ・・・
-
2025.08.04
長尺・大径シャフトの加工における3つのポイント|なぜ大手メーカー中途半端なサイズのシャフトの加工・調達を断るのか?
- シャフト
- 長寿命化
Warning: Undefined variable $news_excerpt_text in /home/xs633096/metal-processing-coordinator.com/public_html/cms/wp-content/themes/hirano-metal/assets/include/part-column-list.php on line 58
長尺・大径シャフトは、産業設備の心臓部を担う重要な部品です。しかし、その加工・調達には、多くの企業が課題を抱えています。
本記事で・・・
-
2025.07.28
S45Cの特徴と加工方法とは?
- 長寿命化
- 表面処理
- 加工
Warning: Undefined variable $news_excerpt_text in /home/xs633096/metal-processing-coordinator.com/public_html/cms/wp-content/themes/hirano-metal/assets/include/part-column-list.php on line 58
S45Cは、機械構造用炭素鋼の代表格として多岐にわたる産業で不可欠な材料です。
本記事では、S45Cの基本的な定義から、その背景、・・・
-
2025.07.25
浸炭焼入れとは?効果、長寿命化への応用まで徹底解説!
- 長寿命化
部品の性能向上や長寿命化は、製造業における永遠の課題です。特に過酷な環境下で使用される金属部品において、その耐久性を高めるための熱処理技術は不可欠と言… -
2025.04.21
サブゼロ処理とは?
- 長寿命化
ゲージや金型といった高精度部品において、微細な寸法変化が製品品質を大きく左右します。焼入れにより鋼材は硬度を得られますが、同時に「見えない変化」が内部… -
2025.03.21
SNC材(ニッケルクロム鋼)のそれぞれの種類と特徴、加工方法まで解説!
- 長寿命化
- 加工
SNC材とは? SNC材(ニッケルクロム鋼)は、高強度・高耐久性を持つ合金鋼の一種であり、自動車部品や産業機械部品など、高負荷がかかる部品の製造に適し… -
2025.01.21
プーリーの摩耗による交換時期の見極め方と頻度を減らすための対策
- プーリー
- 長寿命化
「プーリーの交換時期っていつ頃だろう?」「プーリーの寿命を延ばすにはどうすればいいの?」 製造現場や設備保全を担当されている方なら、一度はこんな疑問を… -
2024.11.19
SCM材(クロムモリブデン鋼鋼材)の特徴と加工方法とは?
- 長寿命化
- 表面処理
- 加工
SCM材(クロムモリブデン鋼鋼材)とは? SCM材は、機械構造用合金鋼の一種で、「クロムモリブデン鋼」とも呼ばれます。この鋼材は、炭素鋼にクロム(Cr… -
2024.11.19
ローラーシャフトとは?用途から選定方法、耐久性向上を実現する方法まで徹底解説!
- シャフト
- 長寿命化
- 丸物部品
- 加工
ローラーシャフトとは? ローラーシャフトは、搬送装置や製造ラインにおいて、物品や部品を円滑に移動させるために使用される円筒形の機械部品です。ローラーシ… -
2024.10.22
歯切り加工とは?
- 長寿命化
- 加工
歯切り加工は、歯車製造において精度と性能を左右する重要な技術です。本コラムでは、歯切り加工の基本から創成法と成形法の違い、歯すじ修正の重要性、そしてギ… -
2024.10.22
ギヤの定義から種類・製造加工まで
- ギヤ
- 長寿命化
- 加工
ギヤは、多くの機械装置において中心的な役割を果たす部品であり、その重要性は非常に大きいです。ギヤは、動力の伝達や速度の変換、トルクの調整など、機械の基… -
2024.10.22
油圧シリンダーピストンの役割と長寿命化の秘訣とは?
- シャフト
- 長寿命化
- 加工
油圧シリンダーは、さまざまな産業で重要な役割を果たすアクチュエータの一つであり、コンパクトなサイズにもかかわらず大きな力を発揮することができる点が特徴… -
2024.07.26
ギヤシャフトの加工方法から長寿命化のポイントまで
- シャフト
- 長寿命化
- 加工
ギヤシャフトとは? ギヤシャフトは、シャフト(軸)にギア(歯車)形状を付加した機械部品です。歯車の刃が切ってあるため、歯切りシャフトとも呼ばれます。ギ… -
2024.07.26
Vプーリーの特徴から加工技術について
- プーリー
- 長寿命化
- 加工
ベルトと共に用いられるプーリーは動力伝達に用いられる円盤状の部品です。 代表的なプーリーの種類には、Vプーリーと歯付きプーリーがあります。 ①Vプーリ…